Feature Articles: NTT Group’s Initiatives for Creating New Value in the Food and Agriculture Sector
1. Environment surrounding food-waste recycling
One of the keys to achieve carbon neutrality and a circular economy in the food and agriculture field is effectively utilizing the large amount of food waste generated every day. While it is important to reduce food loss by minimizing food waste as much as possible, it is effective to utilize food waste as a resource, rather than simply incinerating it.
The two most common approaches to recycling food waste have been conversion to animal feed (“ecofeed”) and conversion to fertilizer (“composting”); however, the business environment surrounding both approaches has become increasingly difficult. The hurdle for ecofeed has been rising every year as sanitary standards have been tightened to counter swine fever and other infectious diseases affecting livestock. As a result, the number of processable waste has diminished, and investment in new equipment is often required to meet sanitary standards. Demand for compost is also an issue. Although some people prefer inexpensive compost due to rising chemical fertilizer prices, as the number of farmers continues to decline, chemical fertilizers—which have a higher fertilizing effect per unit amount and require less labor to apply—are gaining ground, and compost is generally oversupplied. It is thus becoming increasingly common that the more high-quality compost is produced, the more the compost business goes into the red.
In light of the above situation, a third approach to recycling food waste, methanization, has been attracting attention. Methanization is a technology for (i) fermenting and decomposing organic matter through the action of methanogens (microorganisms that produce methane) and (ii) extracting biogas (consisting mainly of methane) produced in that process. The collected biogas can either be burned in dedicated water heaters and boilers for use as hot water or it can be used to produce electricity through biogas generators; consequently, product demand after recycling is not a concern. With the preferential treatment under Japan’s feed-in tariff scheme and the strengthening efforts toward carbon neutrality in public and private sectors, the use of methanization has been rapidly increasing.
2. Issues facing methanization and biogas plants
To further expand the use of methanization, the cost of constructing facilities and the time and effort required for operating and managing them are issues that must be addressed. From both a technical standpoint to ensure stable fermentation of methane and an economic standpoint to increase efficiency of capital investment through economies of scale, it has been common to construct large methane fermentation facilities (biogas plants) with a daily throughput (biostock input) of 50 to 300 tons. Skilled operation managers are often assigned to each facility to monitor the activity of the methanogens and maintain stable fermentation.
Large-scale biogas plants have the advantage of being able to process large amounts of food waste at a time; however, they face two problems. First, as waste-treatment facilities, they can only be installed in a limited number of suitable locations. Second, large amounts of food waste must be transported to them every day, which incurs a high cost and emits carbon dioxide. To further promote food-waste recycling through methanization, it is required to (i) scale-down biogas plants and install them on-site at the location where food waste is discharged, for example, at food-processing plants and large-scale shopping complexes, and (ii) innovate a plant-operation system that enables an ordinary worker to operate the plant easily.
3. Overview and features of a container-type biogas plant and remote-monitoring system
With the above issues and requirements in mind, Biostock CORPORATION developed a container-type biogas plant in collaboration with Vioce Co., Ltd. (Fig. 1). This biogas plant has two key features. It is ultra-compact and easy to operate and is equipped with a remote monitoring system that allows unmanned operation.
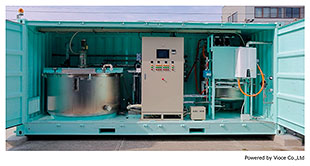
Fig. 1. Container-type biogas plant.
Conventional biogas plants require large-scale construction at each installation site, and it generally takes about two to three years from the start of construction to the start of operation. In contrast, the components required for the container-type biogas plant—as its name implies—are housed in several 20-foot marine shipping containers, so it is remarkably compact. Components of the biogas plant are manufactured at factories. They are then transported to the installation site on a trailer and installed with a crane (Fig. 2). The only on-site work required is connecting electricity and water, so trial operations can begin in as little as two days. The portable nature of the plant also makes it suitable for remote islands and overseas locations where construction work is difficult to arrange.
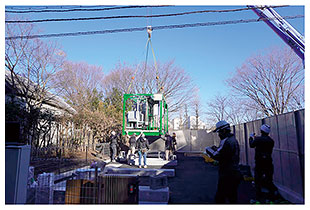
Fig. 2. Installation work for the container-type biogas plant.
The basic configuration of the container-type biogas plant is the same as a conventional biogas plant (Fig. 3). First, the organic waste (biostock) is homogenized in a conditioning tank. It then undergoes a fermentation process using methanogens in a fermentation tank, and biogas is extracted as a renewable energy source. The fermentation residue (digestive liquid) is used for agriculture or purified before being discharged. The container-type biogas plant differs from a conventional plant in that each component is significantly scaled down. By selecting the optimum components in accordance with the volume of biostock to be processed, the increase in system cost can be curtailed, and the components are positioned so that they can be housed in 20-foot containers. This configuration allows the container-type biogas plant to operate with as little as 1 ton of biostock per day, whereas a conventional biogas plant typically requires 50 tons or more per day.
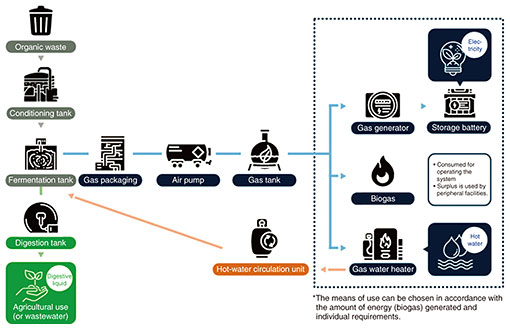
Fig. 3. Configuration of the container-type biogas plant.
The other feature of the container-type biogas plant is its remote monitoring system that enables on-site installation and unattended operation. Conventional large biogas plants generally require a dedicated operation manager at each plant. In contrast, thanks to automatic control and remote monitoring from Biostock by using numerous sensors, the container-type biogas plant can be easily operated and managed without a skilled operation manager at the site where the biostock is discharged.
Although systems for checking the operating status of a biogas plant via control panels at the site and, in some cases, alerts by email are conventionally available, Biostock’s remote monitoring system differs significantly from those conventional systems in terms of economic efficiency, scalability, and security. The system is cloud-based, i.e., not on-premises software, and uses an Internet of Things (IoT) software package with a proven track record in the manufacturing industry. Thus, it is inexpensive and highly scalable. The system is also designed in line with NTT Group’s security guidelines, which ensures it is safe and secure in response to, for example, cyber-attacks in the industrial sector, which are expected to increase in the future. This system will be provided for not only container-type biogas plants supplied by Biostock but also biogas plants supplied by other companies and can be customized in accordance with user requests.
4. Demonstration of the container-type biogas plant at NTTe-City Labo
To verify the usefulness of the developed container-type biogas plant, in collaboration with NTT EAST, Biostock installed the plant at a demonstration field called NTTe-City Labo in February 2022 and started demonstrating an urban-circular ecosystem, of which the plant is a part, that generates energy and fertilizer by using leftover food from the cafeteria of NTT EAST headquarters in central Tokyo and waste from NTTe-City Labo’s farm fields (Fig. 4).
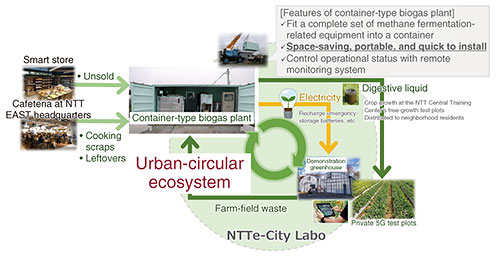
Fig. 4. Overview of the demonstration of an urban-circular ecosystem.
Food scraps and leftovers from the cafeteria at the headquarters of NTT EAST in central Tokyo had been incinerated as general business waste. The container-type biogas plant will process such waste through methanization to achieve food-waste recycling. The collected biogas will be used to generate electricity for recharging emergency-storage batteries in the adjacent greenhouse built to demonstrate state-of-the-art agriculture. It will also be used to power an atmospheric water generator that can extract safe drinking water from the air in times of disaster. We also plan to promote the use of fermentation residue (digestive liquid) as fertilizer, which will be used to grow crops at the NTT Central Training Center (Chofu City, Tokyo). We are also investigating a scheme that uses the fertilizer in community farms and gardens.
Much of the food waste generated by businesses and households is still mostly incinerated without being recycled. Through the above demonstration, we intend to establish an urban-circular ecosystem, of which the container-type biogas plant is a part, that generates energy and fertilizer from urban food waste and use the demonstration as a model to roll out the system nationwide.
The container-type biogas plant installed at NTTe-City Labo is equipped with more sensors and IoT devices than a typical biogas plant; thus, it is possible to remotely monitor the plant and download real-time data, which had not possible without collecting samples and conducting chemical analysis on those samples. Therefore, we intend to implement data analysis that will contribute to the stabilization of fermentation (which is the key to the operation of biogas plants) and demonstrate stable operation through remote management. The results of these analyses and demonstrations will be useful in terms of research on further cost reduction of container-type biogas plants and accumulation of expertise for remote operation and management of these plants.
With the NTT Central Training Center at its core, NTTe-City Labo is a demonstration field where visitors can experience NTT EAST Group’s solutions to local issues and where many cutting-edge technologies including the container-type biogas plant are being tested. An open laboratory for private fifth-generation mobile communication systems (5G) and a demonstration greenhouse for cutting-edge agriculture have been established at NTTe-City Labo. The container-type biogas plant installed there is expected to demonstrate effective use of food waste and local energy production for local consumption and showcase a solution for local issues and smart cities (Fig. 5).
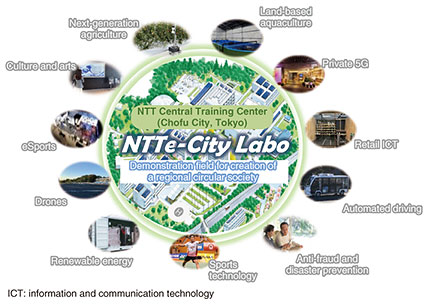
Fig. 5. NTTe-City Labo.
5. Future initiatives and prospects
Starting with the delivery of the container-type biogas plant to NTT EAST, Biostock began marketing and selling container-type biogas plants that are space-saving, portable, and installable in a short time. We expect that container-type biogas plants will be an effective measure for addressing pressing issues concerning businesses that generate organic waste, such as carbon neutrality, decarbonization, and reduction of waste-disposal cost.
Food-processing factories generally produce one to five tons per day of food waste per factory, and it has been difficult to install a biogas plant inside a factory due to the insufficient amount of food waste to be processed and installation space; in contrast, a container-type biogas plant can be installed on-site at the factory without having to meet those requirements. By completing waste disposal, which was previously outsourced, within the factory, it is possible to reduce waste-disposal costs while improving the food-recycling rate. By collecting a renewable energy source, such factories can promote their contribution to achieving the United Nation’s Sustainable Development Goals concerning food.
We also believe that container-type biogas plants can be an effective solution for municipalities struggling with increasing maintenance and operating costs of waste-treatment facilities and sewage-treatment plants. We have heard that many municipalities that separate and collect household food scraps for composting are finding it difficult to continue such operations due to cost burdens. We believe that introducing a container-type biogas plant and shifting to a hybrid process of methanization + composting will drastically improve the balance of payments. It can also be used as a decarbonization initiative in forward-thinking regions to achieve carbon neutrality by 2050.
In its 2021 edition of Annual Report on the Environment, themed “Socioeconomic Redesign toward Carbon Neutrality in 2050,” Japan’s Ministry of the Environment states that the three transitions, i.e., the transition to a decarbonized society, circular economy, and decentralized society, will be key. The container-type biogas plant is truly a solution that meets the needs of the times in terms of renewable-energy generation, recycling, and decentralization of waste disposal (cutting waste transportation). We will use the above demonstration as an opportunity to expand its use throughout Japan.
 |
- Shogo Inoue
- Director, Head of Business Development, Biostock CORPORATION.
|